
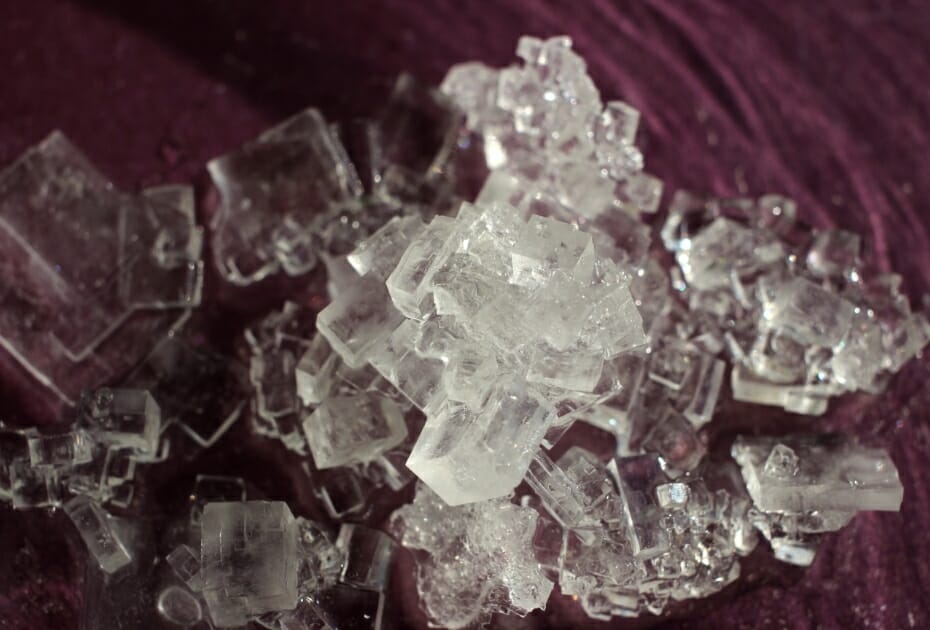
Stages of Manufacturing for the Most Popular Timing Solution
With the ever-changing technological landscape of the world, it has always remained that quartz is the superior material to create clean, long lasting resonators for the most accurate timing products. Almost any material can be capable of generating and resonating frequencies; what makes quartz different is that its unique, crystalline structure allows it to be formed in such a way that results in the most stable resonations.
The process of manufacturing these quartz crystal oscillators is highly specific and difficult to do.
Growing the Artificial Quartz Crystal
Quartz is a naturally occurring mineral with a uniform, crystalline structure that consists of two oxygen atoms and one silicon atom. Years of intense pressure and exposure to high temperatures work to create this unique mineral. The scientific name for this mineral is SiO4 silicon-oxygen tetrahedra.
Unfortunately, nature does not provide the level of constant pressure and the temperatures necessary to grow SiO4 without imperfections and contaminates that would make it unsuitable for use in a technological application. This is where the autoclave steps in. An autoclave is a large pressure vessel that turns raw, natural quartz into a pure bar of SiO4 quartz.
The autoclave puts the raw quartz through pressures around 10,000 psi-40,000 psi, at temperatures of 340~380ºC. Many pieces of quartz, referred to as seeds, are suspended on a wire frame and the autoclave is powered on and pressurized. This results in the natural quartz being evaporated from the bottom, leaving behind any impurities. Following this, the natural quartz reconstitutes onto the seeds while under these constant pressures and temperatures. The process of growing crystals takes anywhere between 30 and 120 days to complete.
Cutting the Crystal
After the autoclave process results in a pure bar of SiO4 quartz, the next step in the manufacturing process is to cut the bar into small pieces, according to the dimensions of its intended use. This is done using high precision cutters that are created to cut very precisely and using exact angles. During this step, manufacturers must remember to make the crystal blanks slightly thicker than required.
These thicker blanks can then be carefully etched and lapped to the required thickness. For more precise crystals, the blank is made slightly thinner in order for it to resonate at a higher frequency that is needed. Following this, a careful process of sputtering gold or other material onto the blank occurs in order to fine tune it to the desired frequency.
Etching
In order to prepare this crystal to be effective in an oscillator, the surface is chemically etched to undo the damage done by lapping. Etching provides a finer finish to the crystal, blocking unwanted chemicals and debris from entering and disrupting frequency. In addition to the fine finish, etching is the last stage in the process that changes the dimension of the crystal. After etching, the crystal should be at the desired size for use.
The etching process must be finished with a careful cleaning of the crystal surfaces, ensuring all traces of the external chemicals used in the etching process are removed.
Electrodes
After the crystal has reached the desired specifications and finish, an electrode base is added by placing the finished crystal blank into an evaporation mask and depositing silver or gold vapor onto the surface of the crystal, forming the electrodes. Lastly, leads are attached to the deposited electrodes and the finished crystal is mounted into its holder.
Sealing
Once the crystal is mounted in its holder, it is hermetically sealed with nitrogen to prevent the entrance of unwanted materials into the design. These unwanted particles can cause aging and other issues within the crystal.
Inspection
The manufacturing process is not complete until the crystal has been fully inspected. During inspection, the crystal should be examined to confirm the specifications are correct and the crystal is operating as intended.
The extent and level of thoroughness in the inspection is dependent on the complexity and desired performance of the crystal. More commonly produced crystals can be inspected in batches, while more nuanced components are usually inspected individually.
ECS Inc. Is Here to Assist You on Your Search for Reliable Timing Solutions
ECS Inc. has over 40 years of experience crafting high quality electronic components including:
For more information, contact an ECS Inc. sales representative in your area or fill out an online contact form.
If you are ready to order your timing solutions or other components, locate one of our authorized distributors in your area on our website to find a trusted partner.
How is My Quartz Oscillator Manufactured? was last modified: February 22nd, 2023 by